Magnetic Destoner
Exl Exports is a leading magnetic separator exporter, specializing in high-quality Magnetic Destoners designed to remove ferrous impurities from various products. Our advanced technology ensures the efficient separation of contaminants such as stones, metallic particles, glass pieces, mud balls, black stones, and other impurities with natural magnetic properties.

Features of Our Magnetic Destoner Machines
Our Magnetic Destoner machines are engineered with precision to deliver optimal performance in separating impurities from various materials. Key features include:
- Versatile Magnetic Roll Sizes: Available in diameters of 75 mm (3 inches), 100 mm (4 inches), 150 mm (6 inches), 200 mm (8 inches), and 240 mm (9.5 inches), with widths up to 2000 mm, accommodating diverse processing requirements.
- Adjustable Speed Drive: Equipped with a 0.5 HP variable speed DC/AC geared motor, allowing roll speed adjustments from 0 to 280 RPM for precise control over the separation process.
- High-Quality Vibratory Feeder: Incorporates a vibratory feeder powered by unbalanced vibratory motors, ensuring consistent and uniform material feeding onto the conveyor belt.
- Durable Conveyor Belts: Fitted with abrasion-resistant endless conveyor belts, 0.35 mm thick, designed to withstand continuous operation and extend equipment lifespan.
These features collectively enhance the efficiency and reliability of our Magnetic Destoner machines, making them an ideal choice for industries seeking effective solutions for impurity separation.
Working Principle
- The Magnetic Destoner employs a conveyor belt system that passes material over a high-intensity magnetic roll. As the material feeds onto the belt, ferromagnetic and paramagnetic particles are attracted to the magnetic roll, adhering to its surface. In contrast, non-magnetic particles continue their trajectory and discharge freely off the end of the conveyor. This process effectively separates magnetic impurities from the desired product, enhancing overall purity and quality.
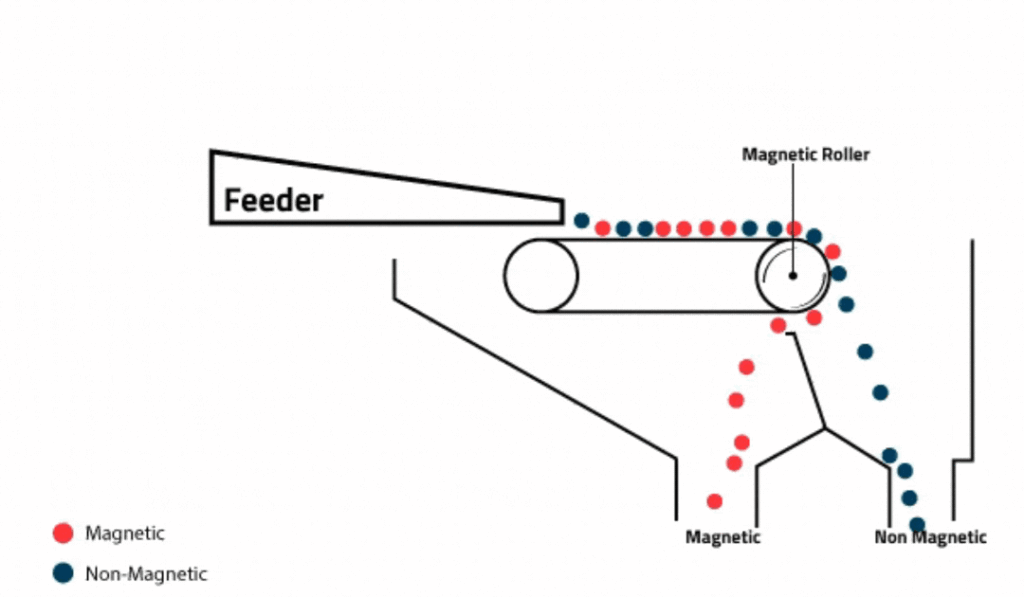
Applications
Our Magnetic Destoner machines are engineered to serve a diverse range of industries, ensuring the removal of impurities and enhancing product quality across various applications.
Mineral Processing Industry:
In the mineral processing sector, our Magnetic Destoners are utilized for:
- Abrasive, Refractory, and Ceramic Raw Material Beneficiation: Enhancing the purity of materials such as alumina, silica, carbide, magnesite, and quartzite.
- Glass Raw Materials Cleaning: Purifying silica, quartz, feldspar, and dolomite to meet stringent quality standards.
- Ultra High Purity Quartz Cleaning: Achieving exceptional levels of purity required for specialized industrial applications.
- Graphite Upgrading: Improving the quality and value of graphite through effective impurity removal.
- Manganese Ore Beneficiation: Separating magnetic impurities to enhance manganese ore quality.
- Bauxite Upgrading: Refining bauxite by eliminating unwanted magnetic particles.
- Diamond Ore Beneficiation: Assisting in the extraction of diamonds by removing ferrous contaminants.
- Selective Separation of Garnet, Ilmenite, Rutile, and Zircon: Facilitating the concentration of valuable minerals through precise magnetic separation.
- Iron Ore Beneficiation: Enhancing iron ore quality by removing magnetic impurities.
- Recovery of Metals from Slag: Extracting valuable metals from industrial slag waste.
- Removal of Ferrous Silicates from Limestone and Magnesite: Improving the purity of these materials for industrial use.
Food Processing Industry:
In the food processing industry, our Magnetic Destoners play a crucial role in ensuring product safety and quality by removing impurities such as mud balls, black stones, and other contaminants from various food products.
Key applications include:
Grain Cleaning: Purifying wheat, rice, and semolina to ensure they are free from impurities.
Seed Cleaning: Removing contaminants from sesame, cumin, and fennel seeds to maintain product integrity.
Spice Processing: Ensuring the purity of chili flakes and other spices by eliminating unwanted particles.
By integrating our Magnetic Destoner machines into your processing lines, you can achieve higher product quality, comply with industry standards, and protect downstream equipment from potential damage caused by impurities.
Usage of Magnetic Destoner Machines
Our Magnetic Destoner machines are essential for enhancing product purity across various industries. Key applications include:
- Grain Cleaning: Effectively removes impurities from rice, wheat, corn, pulses, semolina, and seeds such as sesame, cumin, and fennel.
- Spice Processing: Ensures the cleanliness of spices like chili flakes, maintaining high-quality standards.
- Post-Gravity Separation: Provides an additional layer of purification following gravity separation processes.
- Integration with Bucket Elevators: Installed at the discharge points to capture and remove ferrous contaminants.
- Flour Milling: Positioned at the initial break in flour mills to eliminate unwanted particles, ensuring superior flour quality.
- Cleaning Lines: Incorporated into various stages of cleaning lines to maintain product integrity.
- Automated Cleaning Systems: Compatible with auto-cleaning machines, enhancing overall operational efficiency.
By integrating our Magnetic Destoner machines into your processing lines, you can achieve higher product quality, comply with industry standards, and protect downstream equipment from potential damage caused by impurities.
Frequently Asked Questions (FAQ)
Our Magnetic Destoner machines are designed to enhance product purity by effectively removing impurities from various materials. Here are some common questions and answers to help you understand their functionality and applications:
1. What is a Magnetic Destoner?
A Magnetic Destoner is a device that uses magnetic fields to separate ferromagnetic and paramagnetic impurities from materials such as grains, spices, and pulses, ensuring higher product purity.
2. How does a Magnetic Destoner work?
The machine consists of a conveyor belt that passes material over a high-intensity magnetic roll. Ferromagnetic and paramagnetic particles are attracted to the magnetic roll and separated from non-magnetic particles, which continue off the end of the conveyor.
3. What types of impurities can the Magnetic Destoner remove?
It effectively removes impurities like mud balls, black stones, metallic fragments, glass pieces, and other contaminants with magnetic properties from various materials.
4. In which industries can the Magnetic Destoner be used?
Our Magnetic Destoner is suitable for flour mills, rice mills, dal mills, food processing units, and any industry requiring the separation of impurities from food products.
5. What are the available sizes of Magnetic Rolls?
Magnetic Rolls are available in diameters of 75 mm (3 inches), 100 mm (4 inches), 150 mm (6 inches), 200 mm (8 inches), and 240 mm (9.5 inches), with widths up to 2000 mm, accommodating diverse processing requirements.
6. What is the capacity range of the Magnetic Destoner?
Our Magnetic Destoners have a capacity range starting from 1 metric ton to 30 metric tons per hour for wheat and other commodities. We can design machines to meet specific capacity requirements.
7. How is the speed of the magnetic roll controlled?
The machine is equipped with a 0.5 HP variable speed DC/AC geared motor, allowing roll speed adjustments from 0 to 280 RPM for precise control over the separation process.
8. What maintenance is required for the Magnetic Destoner?
Regular maintenance includes cleaning the magnetic elements to prevent buildup of suspended solids and checking mechanical components for imbalances or vibrations to ensure smooth operation.
9. Can the Magnetic Destoner be integrated into existing processing lines?
Yes, our Magnetic Destoners are designed with a compact footprint and can be integrated into existing processing lines, including installations at the discharge of bucket elevators, after gravity separations, and in cleaning lines.